A Comprehensive Overview to the Process and Advantages of Plastic Extrusion
In the large world of production, plastic extrusion arises as a important and highly effective process. Transmuting raw plastic into continual accounts, it provides to a huge selection of industries with its exceptional convenience.
Recognizing the Basics of Plastic Extrusion
While it might appear complicated at very first glimpse, the process of plastic extrusion is essentially basic. The process begins with the feeding of plastic material, in the type of granules, powders, or pellets, right into a heated barrel. The designed plastic is after that cooled down, solidified, and reduced right into wanted sizes, finishing the process.
The Technical Process of Plastic Extrusion Explained
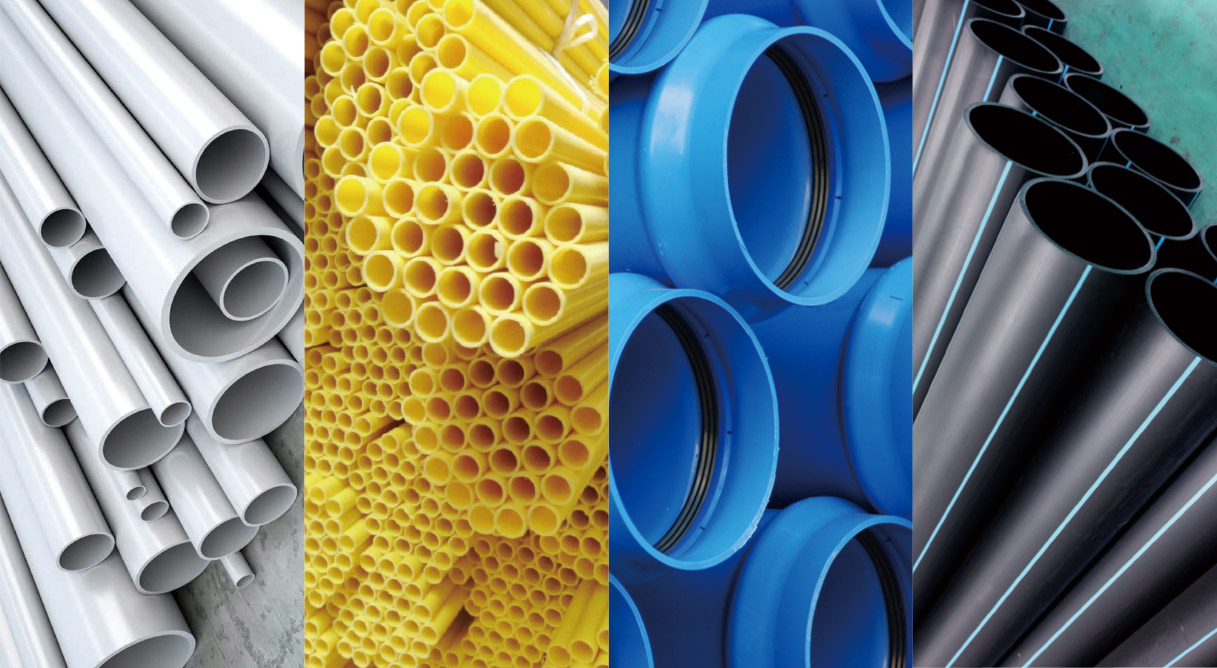
Kinds Of Plastic Suitable for Extrusion
The selection of the ideal kind of plastic is an important element of the extrusion process. Numerous plastics provide unique residential or commercial properties, making them more fit to specific applications. Polyethylene, for instance, is commonly made use of because of its inexpensive and easy formability. It uses exceptional resistance to chemicals and wetness, making it optimal for products like tubing and containers. Polypropylene is one more preferred option due to its high melting factor and resistance to tiredness. For even more robust applications, polystyrene and PVC (polyvinyl chloride) are usually picked for their strength and sturdiness. These are common options, the choice eventually depends on the details demands of the product being produced. So, understanding these plastic types can dramatically improve the extrusion procedure.
Comparing Plastic Extrusion to Various Other Plastic Forming Approaches
Understanding the types of plastic ideal for extrusion leads the method for a more comprehensive conversation on how plastic extrusion piles up against various other plastic developing methods. Plastic extrusion is unparalleled when it comes to creating continuous profiles, such as seals, pipelines, and gaskets. It likewise permits for a regular cross-section along the size of the product.
Secret Benefits of Plastic Extrusion in Production
In the world of production, plastic extrusion uses lots of substantial advantages. One noteworthy advantage is the cost-effectiveness of the procedure, that makes it a financially attractive manufacturing technique. Additionally, this method offers remarkable item versatility and enhanced production speed, thus enhancing general manufacturing performance.
Affordable Manufacturing Approach
Plastic extrusion leaps to the center as a cost-effective production technique in manufacturing. This process attracts attention for its capability to produce high quantities basics of product rapidly and successfully, providing manufacturers with significant cost savings. The primary expense advantage is the capacity to use less pricey resources. Extrusion utilizes thermoplastic products, which are less pricey compared to metals or porcelains. Further, the extrusion process itself is reasonably straightforward, decreasing labor prices. In addition, plastic extrusion needs less energy than standard production approaches, adding to lower operational expenses. The process additionally reduces waste, as any kind of excess or defective materials can be recycled and recycled, supplying another layer of cost-effectiveness. On the whole, the financial advantages make plastic extrusion an extremely eye-catching option in the manufacturing market.
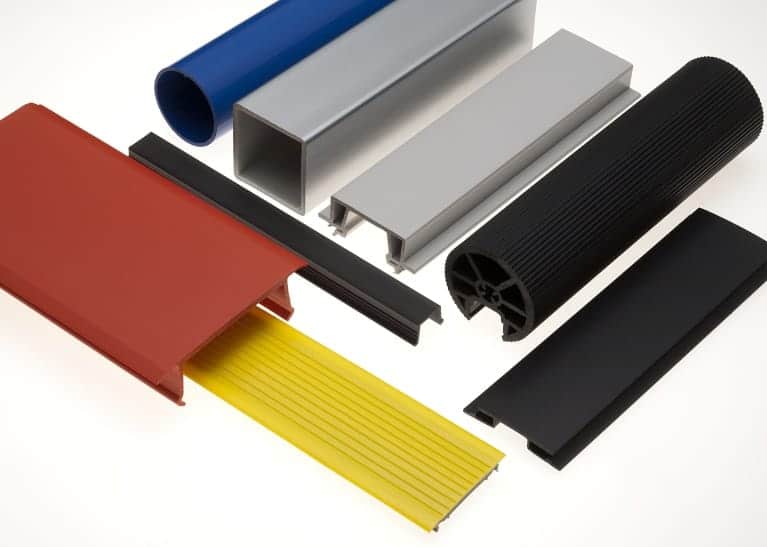
Superior Item Adaptability
Past the cost-effectiveness of plastic extrusion, one more significant advantage in making lies in its premium product flexibility. This makes plastic extrusion a perfect service for sectors that need tailored plastic parts, such as automotive, construction, and packaging. In significance, visite site plastic extrusion's item versatility promotes development while improving functional performance.
Boosted Manufacturing Speed
A considerable benefit of plastic extrusion exists in its boosted manufacturing speed. Couple of other manufacturing procedures can match the speed of plastic extrusion. In addition, the capacity to keep constant high-speed manufacturing without giving up product quality establishes plastic extrusion apart from other techniques.
Real-world Applications and Effects of Plastic Extrusion
In the world of production, the method of plastic extrusion holds extensive significance. This procedure is extensively utilized in the production of a range of products, such as plastic tubes, window frames, and climate removing. Consequently, it greatly affects markets like construction, product packaging, and auto markets. Additionally, its impact encompasses daily products, from plastic bags to toothbrushes and non reusable flatware. The economic advantage of plastic extrusion, primarily its cost-effective and high-volume outcome, has actually reinvented manufacturing. The ecological influence of plastic waste remains a problem. For that reason, the sector is persistently pursuing developments in recyclable and eco-friendly products, suggesting a future where the advantages of plastic extrusion can be retained without Source compromising ecological sustainability.
Verdict
To conclude, plastic extrusion is a highly effective and effective approach of changing raw materials into varied items. It uses various benefits over various other plastic developing methods, consisting of cost-effectiveness, high result, marginal waste, and layout adaptability. Its effect is exceptionally felt in numerous sectors such as building, auto, and consumer items, making it a pivotal procedure in today's manufacturing landscape.
Delving deeper into the technological procedure of plastic extrusion, it starts with the selection of the proper plastic material. As soon as cooled, the plastic is cut into the required sizes or injury onto reels if the item is a plastic movie or sheet - plastic extrusion. Contrasting Plastic Extrusion to Other Plastic Forming Methods
Understanding the types of plastic appropriate for extrusion leads the way for a more comprehensive discussion on how plastic extrusion piles up against other plastic developing approaches. Few various other manufacturing processes can match the speed of plastic extrusion.